Silicone Membrane for Vacuum Forming: A Comprehensive Guide
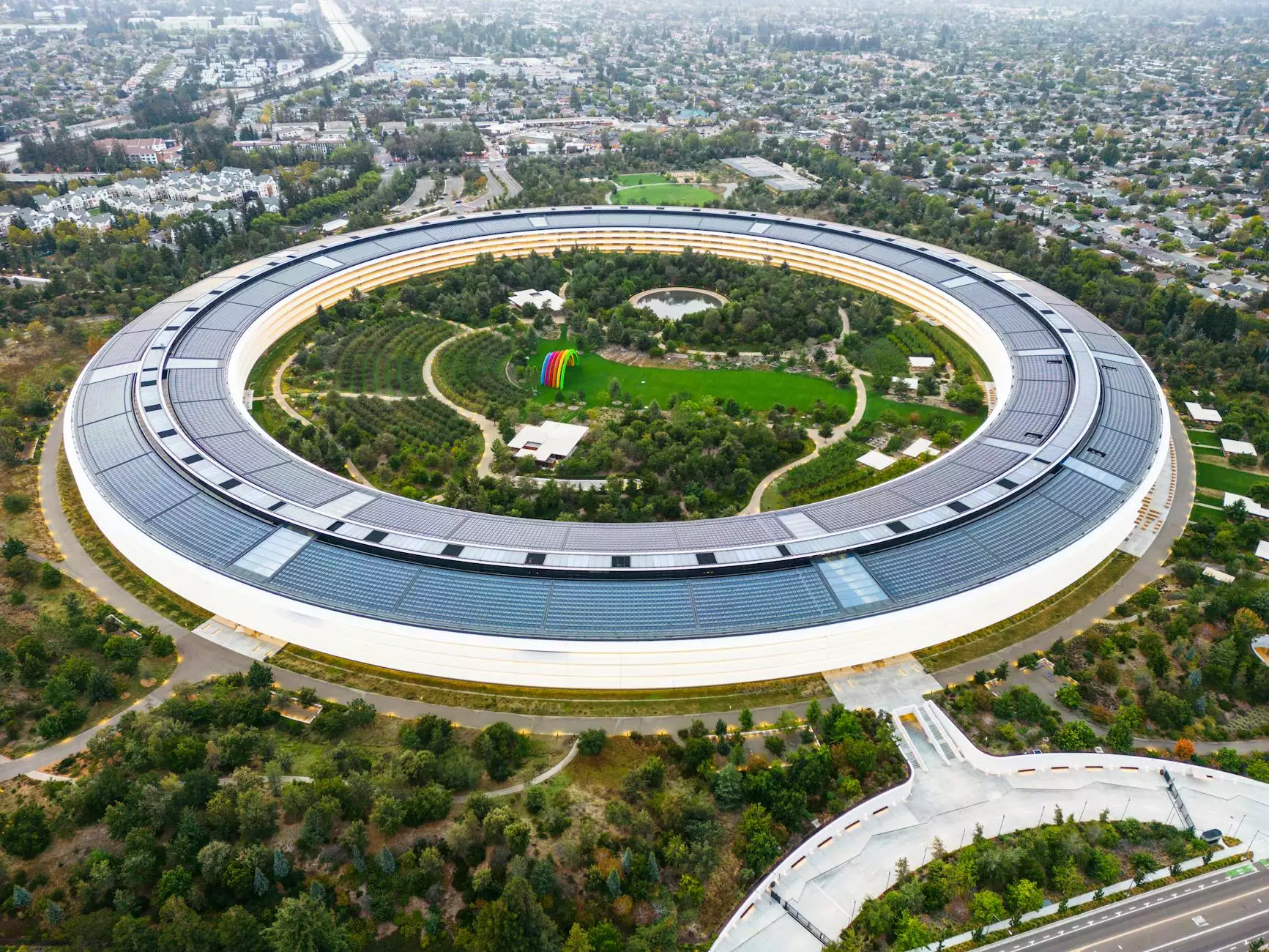
In the realm of vacuum forming, one of the most crucial components is the silicone membrane. This innovative material plays a vital role in achieving efficient and high-quality production across multiple industries. In this article, we will delve into the significance of silicone membranes, their applications, advantages over rubber membranes, purchasing guidance, and more.
Understanding Vacuum Forming
Vacuum forming is a manufacturing process where a plastic sheet is heated until pliable, then formed over a mold using vacuum pressure. This method is widely utilized for producing components in sectors such as automotive, packaging, and consumer goods. The effectiveness of this process heavily relies on the type of membrane used in conjunction with the vacuum system.
What is a Silicone Membrane?
A silicone membrane is a flexible, durable layer made from high-quality silicone that can withstand varying temperatures and pressures. Its unique properties make it an excellent choice for vacuum forming applications.
Properties of Silicone Membranes
- Temperature Resistance: Silicone membranes can operate effectively in a wide range of temperatures, typically from -60°C to +200°C.
- Durability: With excellent tear strength and flexibility, silicone membranes can endure repetitive use without significant wear or damage.
- Chemical Resistance: They are resistant to a variety of chemicals, making them suitable for many industrial applications.
- Non-Stick Surface: Silicone has inherently non-stick properties, allowing for easy release of formed parts.
Why Choose Silicone Membranes for Vacuum Forming?
Using a silicone membrane for vacuum forming has several advantages over traditional rubber membranes. The benefits include:
1. Enhanced Forming Quality
The flexibility and conformability of silicone membranes allow for superior detail reproduction. This characteristic is vital in sectors where precision is paramount.
2. Longer Lifespan
Silicone membranes generally have a longer operational lifespan than rubber counterparts, leading to reduced costs associated with replacements and maintenance.
3. Better Temperature Management
Silicone’s high-temperature tolerance ensures effectiveness even in demanding environments, making it a reliable choice for high-heat applications.
4. Easy Maintenance
The non-stick nature of silicone means that cleanup is often easier, and the risk of product adhesion is minimized.
Applications of Silicone Membranes in Various Industries
Silicone membranes are utilized in a variety of sectors, showcasing their versatility. Some key industries include:
1. Automotive Manufacturing
In the automotive sector, silicone membranes are used to create dashboards, panels, and other interior components that require intricate detailing and durability.
2. Food Packaging
The food industry benefits from silicone’s inert properties, which comply with health regulations. Silicone membranes are employed in vacuum packaging to preserve food quality.
3. Consumer Electronics
Silicone membranes are crucial in the production of electronic casings and protective components, providing both physical protection and aesthetic appeal.
4. Medical Devices
In the medical field, silicone's biocompatibility makes it an ideal choice for manufacturing devices that require strict sanitary conditions and reliability.
Buying Silicone Membranes: Factors to Consider
When looking to buy silicone membranes, several factors should be evaluated to ensure you select the best product for your needs:
1. Quality of Material
High-quality silicone should be flexible, durable, and resistant to wear. Verify the supplier’s reputation and product specifications.
2. Thickness and Size
Choose the right thickness and size based on your specific application requirements. Thicker membranes might be necessary for certain molds or processes.
3. Temperature Ratings
Ensure that the silicone membrane can handle the temperature range required for your vacuum forming applications.
4. Supplier Reliability
Opt for reputable suppliers like vacuum-presses.com that specialize in vacuum system parts, including silicone membranes, rubber membranes, and natural rubber membranes.
Conclusion
In conclusion, the silicone membrane for vacuum forming is an indispensable component that enhances the efficiency and quality of produced items across various industries. Its unique properties set it apart from traditional materials, making it a preferred choice for manufacturers looking to optimize their processes.
For those interested in implementing this technology or purchasing silicone membranes, explore options at vacuum-presses.com to find high-quality products tailored for your needs.
Frequently Asked Questions
1. How long do silicone membranes last?
With proper care and maintenance, silicone membranes can last significantly longer than rubber membranes, often enduring multiple production cycles without degrading in performance.
2. Can silicone membranes be used for high-temperature applications?
Yes, silicone membranes are highly resistant to heat and can be used effectively in high-temperature vacuum forming applications.
3. Where can I purchase silicone membranes?
You can purchase silicone membranes from specialized suppliers, such as vacuum-presses.com, which offers a range of vacuum system parts.
4. Are silicone membranes environmentally friendly?
Silicone is considered more environmentally friendly compared to other plastics, as it is derived from natural materials and can often be recycled.