Unlocking the Potential of Custom CNC Machining in Metal Fabrication
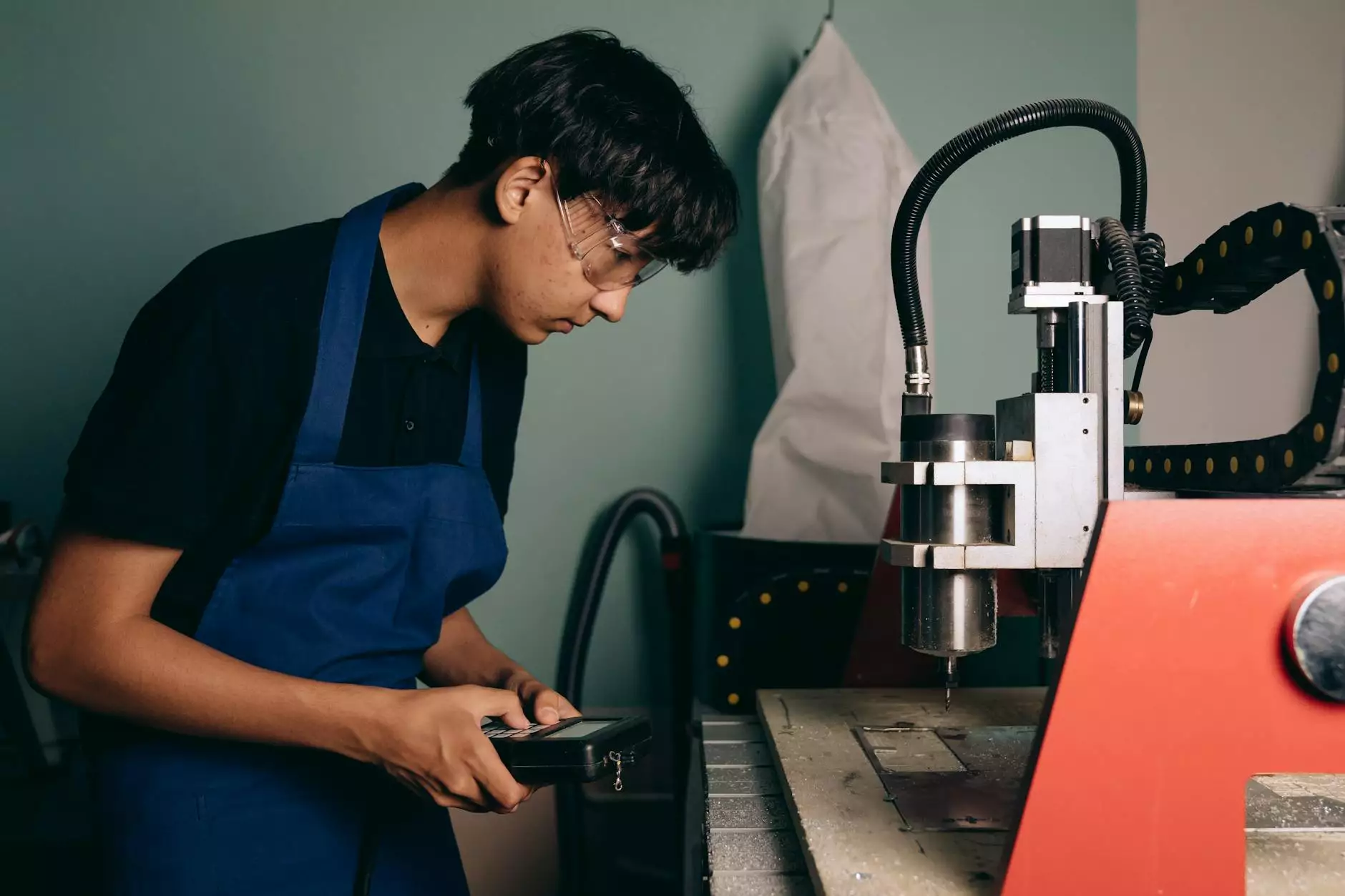
Custom CNC machining has revolutionized the landscape of manufacturing and metal fabrication. As industries evolve and demand for precision and efficiency escalate, custom CNC machining stands at the forefront, blending innovative technology with unparalleled craftsmanship. This article delves into the nuances of custom CNC machining, exploring its advantages, applications, and the transformative impact it holds for businesses in the metal fabrication sector.
What is Custom CNC Machining?
CNC, or Computer Numerical Control, machining refers to the automated control of machining tools through programmed commands. These commands are executed via a computer, allowing for high precision and repeatability in fabricated parts. Custom CNC machining takes this concept further by tailoring the machining process to meet specific client requirements, engaging in intricate and complex designs that are often impossible with traditional machining methods.
The Advantages of Custom CNC Machining
Businesses across various industries benefit significantly from custom CNC machining. Here are some primary advantages:
- Precision and Accuracy: CNC machines can consistently produce parts with minimal tolerances, often in the realm of thousandths of an inch.
- Scalability: Custom CNC machining easily scales to produce small runs of unique components or large batches of identical items.
- Versatility: Capable of working with various materials, including metals, plastics, and composites, CNC machining can accommodate a wide array of projects.
- Increased Efficiency: Automated processes reduce manual labor input, enabling faster production times without sacrificing quality.
- Complex Geometries: CNC machines can create intricate designs and complex geometries that would be challenging to achieve through manual methods.
Understanding the CNC Machining Process
The CNC machining process involves several key steps:
- Design Phase: The product design is created using CAD (Computer-Aided Design) software, allowing for precise visualization of the final component.
- Conversion to G-Code: The CAD file is then translated into G-Code, a language that CNC machinery understands, containing the exact movements and commands needed.
- Machine Setup: The CNC machine is set up with the appropriate tools, fixtures, and raw materials as per the product specifications.
- Machining: The CNC machine begins the automated machining process, employing tools to cut, shape, and finish the material based on the programmed commands.
- Quality Control: Finished components undergo rigorous inspection to ensure conformity to design specifications and quality standards.
Applications of Custom CNC Machining
Given its versatility and precision, custom CNC machining finds applications across various sectors:
Aerospace Industry
The aerospace industry demands high-performance components where safety and reliability are paramount. Custom CNC machining allows for producing lightweight yet durable parts that adhere to strict regulatory standards.
Automotive Sector
In automotive manufacturing, custom CNC machining plays a critical role in developing intricate engine parts, transmission components, and more, ensuring optimal performance and longevity.
Medical Devices
The demand for precision in medical devices cannot be overstated. Custom CNC machining facilitates the production of surgical instruments, prosthetics, and dental devices, allowing for tailored solutions that meet specific patient needs.
Electronics
Custom CNC machining allows for precise housings and components in the electronics sector, where design specifications are often intricate and require higher standards of detail.
Choosing the Right CNC Machining Partner
Selecting a competent partner for custom CNC machining is crucial for your business’s success. Look for these factors when choosing a CNC machining company:
- Experience: An established company with a proven track record ensures expertise in handling complex projects.
- Quality Certifications: Certifications such as ISO 9001 indicate a commitment to quality assurance and adherence to industry standards.
- Technological Capability: Advanced machinery and up-to-date software ensure that the CNC machining process is efficient and precise.
- Customer Service: A reliable partner communicates effectively, providing support and guidance throughout the project lifecycle.
- Customization Options: The ability to tailor solutions based on your specific needs is essential for ensuring satisfaction.
Future Trends in Custom CNC Machining
As technology continues to advance, several trends are shaping the future of custom CNC machining:
Integration of AI and Machine Learning
The incorporation of artificial intelligence (AI) and machine learning in CNC machining allows for predictive maintenance and optimized machining processes, reducing downtime and enhancing efficiency.
Adoption of Additive Manufacturing
Combining CNC machining with additive manufacturing (3D printing) provides a synergistic approach, allowing for the creation of complex geometries with more design freedom.
Enhanced Software Solutions
Advanced software solutions are improving design capabilities, simulation, and operator training, resulting in better overall efficiency and quality control.
Conclusion
Custom CNC machining is not merely a manufacturing process; it is a cornerstone of modern industry that empowers businesses to innovate and excel. By understanding its intricacies and applications, companies can harness the potential of custom CNC machining to produce high-quality, precise parts that fulfill the evolving demands of the market. At deepmould.net, we excel in providing custom CNC machining services tailored to your needs, ensuring quality, precision, and excellence at every step.
In a competitive landscape, investing in custom CNC machining not only enhances production capabilities but also positions your business for future growth and success.
© 2023 Deep Mould. All rights reserved.