Understanding Central Lubrication System Fittings
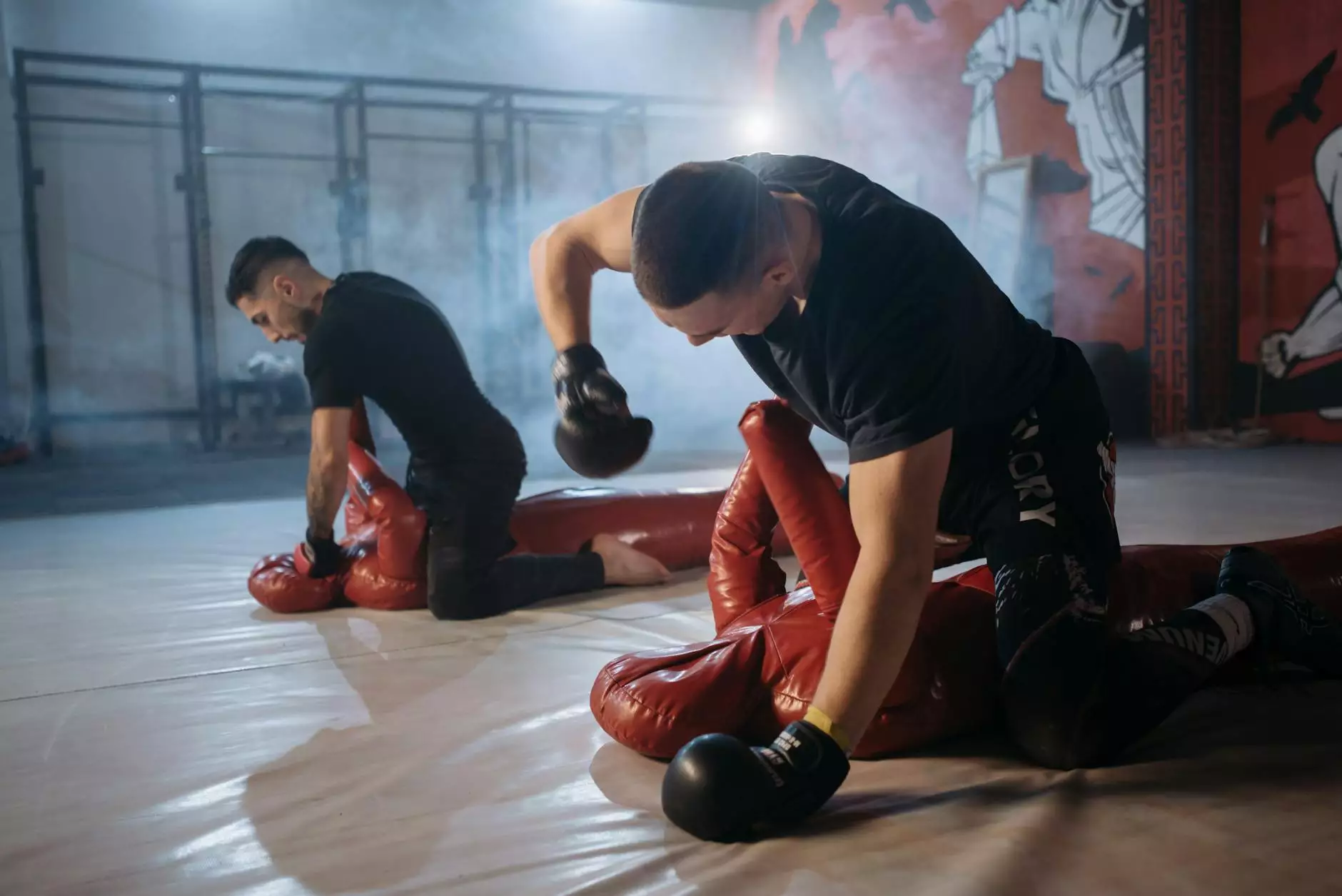
The importance of maintaining machinery in top working condition cannot be overstated. A central lubrication system is a vital component in ensuring the longevity and efficiency of various machines. In this article, we will explore central lubrication system fittings, their role, types, benefits, and how to choose the right fittings for your specific needs.
What is a Central Lubrication System?
A *central lubrication system* is designed to provide lubrication to multiple points on a machine or an assembly in an automated manner. This sophisticated system reduces the need for manual lubrication, minimizes downtime, and enhances productivity. By maintaining optimal lubrication, a central system prevents wear and tear, reducing the risk of breakdowns and extending the life of equipment.
Key Components of Central Lubrication Systems
Several components make up a central lubrication system, each playing a crucial role in its operation:
- Lubrication Pump: This pump delivers the lubricant to the various lubrication points in the system.
- Reservoir: A storage unit for lubricants, ensuring an uninterrupted supply.
- Control Panel: This allows the operator to monitor and control the system.
- Lubrication Lines: These are the conduits through which the lubricant travels to reach designated points.
- Fittings: These connect the lubrication lines to the components requiring lubrication.
Importance of Central Lubrication System Fittings
Central lubrication system fittings are critical to the efficient functioning of any lubrication system. They ensure that the lubricant reaches the necessary components effectively and without leakage. The proper fitting guarantees the integrity of the lubrication line, maintaining pressure and flow rate necessary for optimal performance.
Types of Central Lubrication System Fittings
There are various types of fittings available for central lubrication systems. Understanding these can help you make informed decisions when selecting the right fittings for your application:
- Threaded Fittings: Ideal for permanent connections, threaded fittings create a tight seal and are commonly used in high-pressure applications.
- Push-On Fittings: These provide a quick and easy means of connecting lubrication lines. They're ideal for temporary installations.
- Flared Fittings: Commonly used in high-pressure environments, flared fittings ensure a secure connection by creating a wider contact area.
- Compression Fittings: These are utilized for reliable connections without requiring the threads; ideal for intricate layouts.
- Swivel Fittings: These components allow for the reorientation of the lubrication lines without compromising the seal, which is essential in tight spaces.
Advantages of Using Central Lubrication System Fittings
Investing in quality central lubrication system fittings brings numerous advantages:
- Increased Efficiency: Automated systems reduce labor and time spent on lubrication.
- Reduced Wear and Tear: Ensures consistent lubrication, minimizing friction and prolonging machinery life.
- Lower Maintenance Costs: By preventing equipment failure, you save on repairs and downtime.
- Improved Safety: Automated systems decrease the risk of human error in lubrication processes.
How to Choose the Right Central Lubrication System Fittings
Selecting the correct fittings for your central lubrication system is crucial for its performance and reliability. Here are some key factors to consider:
1. Compatibility with the Lubricant
Ensure that the materials used for the fittings are compatible with the type of lubricant you plan to use. Some lubes are corrosive and may require fittings made from specific materials like stainless steel.
2. Pressure and Temperature Ratings
Your fittings must be rated for the pressure and temperature limits of your system. Using fittings out of their rating can lead to leaks and system failures.
3. Application Specifics
Consider where the fittings will be used. For example, fittings in challenging environments may require specific designs that resist dust, moisture, or extreme temperatures.
4. Maintenance and Access
Choose fittings that will be easy to maintain and provide the necessary access for servicing. This is crucial in emergency situations where immediate action is required.
Installation of Central Lubrication System Fittings
The installation of central lubrication system fittings should be carried out by skilled professionals to ensure compliance with industry standards and safety protocols. Here are some general steps to follow:
- Preparation: Gather all tools and fittings necessary for the installation.
- Clean the Surface: Ensure that all surfaces are clean to promote a good seal.
- Inspect Fittings: Check the fittings for any damage before installation.
- Install the Fittings: Securely attach the fittings to the lubrication lines, ensuring there are no leaks.
- Test the System: Once installed, run the system to check for functionality and leaks.
Effective Maintenance of Central Lubrication Systems
Regular maintenance of central lubrication system fittings and the entire system is essential for sustained performance:
- Regular Inspections: Consistently check connections, fittings, and lines for signs of wear or leaks.
- Lubricant Changes: Regularly change the lubricant as recommended by the manufacturer.
- Check the Pump: Ensure the pump operates correctly and replaces its components when necessary.
- Cleaning: Maintain cleanliness in all parts of the lubrication system to prevent contamination.
Where to Purchase Quality Central Lubrication System Fittings
For high-quality central lubrication system fittings, consider reputable suppliers such as fitsch.cn. They offer a wide range of fittings designed for various applications, ensuring you find what you need for your machinery.
Conclusion
In conclusion, central lubrication system fittings are an integral part of maintaining efficient and reliable machinery. Choosing the right fittings and maintaining them correctly can lead to significant cost savings, enhanced safety, and improved operational efficiency. By investing in quality components from trusted suppliers, you can ensure the longevity and reliability of your equipment.
Whether you're setting up a new system or replacing existing components, understanding the intricacies of lubrication system fittings will empower you to make informed decisions that benefit your business in the long run.